КАК ПРОЕКТИРОВАТЬ ДЛЯ ПРОИЗВОДСТВА МЕТАЛЛИЧЕСКИХ ДЕТАЛЕЙ ПОРОШКОВОГО
Дорогой друг, вы можете использовать эти советы по проектированию порошковой металлургии, чтобы создать компонент, максимально использующий технологию порошковой металлургии. Это не всеобъемлющее руководство по проектированию деталей из порошкового металла. Однако соблюдение этих рекомендаций повысит эффективность производства и снизит затраты на оснастку. Контакт Jiehuang as компания порошковой металлургии как можно скорее, чтобы мы могли помочь вам получить максимальную отдачу от ваших компонентов из порошкового металла для производства P/M. Вы также можете сравнить производство порошкового металла с другими доступными технологиями производства. Используйте наши знания, чтобы достичь и превзойти свои производственные цели. Для начала немедленно свяжитесь с нами. Наша страсть — проектирование порошковых металлов, и мы можем помочь!
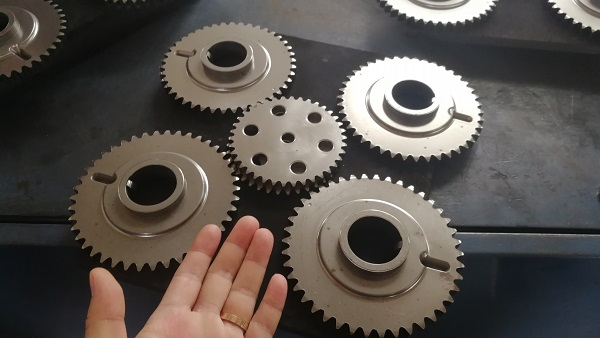
ПОРОШКОВЫЕ МЕТАЛЛИЧЕСКИЕ МАТЕРИАЛЫ
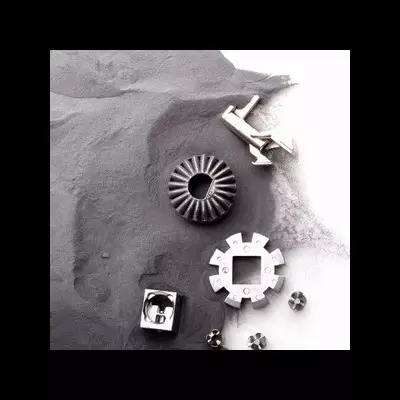
Материалы порошковой металлургии на основе железа
Материалы для порошковой металлургии на основе железа в основном состоят из элементов железа и класса материалов из железа и стали, образованных путем добавления легирующих элементов, таких как C, Cu, Ni, Mo, Cr и Mn. Изделия на основе железа являются наиболее производительным видом материалов в промышленности порошковой металлургии.
1. Порошок на основе железа
Порошки, используемые в порошковой металлургии, материалы и изделия на основе железа в основном включают порошок чистого железа, композитный порошок на основе железа, предварительно легированный порошок на основе железа и т. Д.
2. Изделия из ПМ на основе железа
Обычная технология прессования/спекания обычно позволяет производить изделия на основе железа плотностью 6,4–7,2 г/см3, которые используются в автомобилях, мотоциклах, бытовой технике, электроинструментах и других отраслях промышленности, с преимуществами амортизации, снижения шума, легкий вес и энергосбережение.
3. Порошковое литье под давлением (MIM) изделий на основе железа.
Литье под давлением металлического порошка (MIM) использует металлический порошок в качестве сырья для изготовления небольших металлических деталей сложной формы посредством процесса литья пластмасс под давлением. Что касается материалов MIM, то 70% используемых в настоящее время материалов составляют нержавеющая сталь, а 20% — низколегированные стали. Технология MIM широко используется в производстве мобильных телефонов, компьютеров и вспомогательного оборудования, такого как зажимы для SIM-карт мобильных телефонов, кольца для камер и т. д.
Твёрдый сплав порошковой металлургии
Цементированный карбид представляет собой твердый материал порошковой металлургии с карбидом или карбонитридом тугоплавкого металла переходной группы в качестве основного компонента. Благодаря хорошей прочности, твердости и прочности цементированный карбид в основном используется в качестве режущего инструмента, горнодобывающего инструмента, износостойких деталей, верхних молотков, валков и т. д. и широко используется в сталелитейной, автомобильной, аэрокосмической промышленности, станках с ЧПУ. , машиностроение. Пресс-форма, морское инженерное оборудование, оборудование для железнодорожного транспорта, промышленность электронных информационных технологий, производство и обработка строительной техники и другого оборудования, а также горнодобывающая промышленность, добыча ресурсов нефти и газа, строительство инфраструктуры и другие отрасли.
Магнитный материал для порошковой металлургии
Магнитные материалы, полученные методами порошкового формования и спекания, можно разделить на две категории: постоянные магнитные материалы порошковой металлургии и магнитомягкие материалы. Материалы для постоянных магнитов в основном включают материалы для постоянных магнитов из самария, кобальта, редкоземельных металлов, неодим, железо, материалы для постоянных магнитов из бора, спеченные материалы для постоянных магнитов AlNiCo, ферритовые материалы для постоянных магнитов и т. д. Мягкие магнитные материалы для порошковой металлургии в основном включают мягкий феррит и магнитомягкие композитные материалы.
Преимущество порошковой металлургии для подготовки магнитных материалов заключается в том, что она позволяет готовить магнитные частицы в диапазоне размеров одного домена, достигать постоянной ориентации магнитного порошка в процессе прессования и напрямую производить магниты с высокой магнитной энергией, близкие к конечной форме, особенно для труднообрабатываемых твердых и хрупких магнитных материалов. С точки зрения материалов преимущества порошковой металлургии более заметны.
Суперсплавы порошковой металлургии
Суперсплавы порошковой металлургии основаны на никеле и содержат различные легирующие элементы, такие как Co, Cr, W, Mo, Al, Ti, Nb, Ta и т. д. Они обладают превосходной жаропрочностью, усталостной стойкостью, стойкостью к горячей коррозии и другими комплексными свойствами. характеристики. Сплав является материалом ключевых компонентов горячего конца, таких как валы турбин авиационных двигателей, перегородки дисков турбин и диски турбин. Обработка в основном включает подготовку порошка, термоупрочнение и термообработку.
Наша профессиональная команда проконсультирует по материалам, исходя из свойств ваших деталей из порошкового металла. Одним из основных преимуществ является широкий спектр сырья, которое может быть использовано для удовлетворения ваших потребностей с точки зрения цены, долговечности, контроля качества и конкретных применений. использования порошкового металла для производства компонентов. Железо, сталь, олово, никель, медь, алюминий и титан входят в число часто используемых металлов. Возможно использование тугоплавких металлов, включая бронзу, латунь, нержавеющую сталь и никель-кобальтовые сплавы, а также вольфрам, молибден и тантал. Процесс порошковой металлизации включает в себя объединение различных металлов для создания уникальных сплавов, соответствующих требованиям вашего применения. Мы можем помочь вам в разработке самосмазывания, устойчивости к коррозии и других качеств, которые являются важнейшим компонентом производственного процесса в дополнение к прочности и твердости. Используя эти уникальные смеси металлических порошков, мы можем прессовать сложные конструкции со скоростью производства до 100 деталей в минуту.
Прессование
Его помещают в вертикальный гидравлический или механический пресс, где он помещается в матрицу из инструментальной стали или твердосплавного сплава после смешивания соответствующего сплава порошков. JIEHUANG может штамповать детали с четырьмя различными уровнями детализации. В зависимости от требований к размеру и плотности этот метод использует давление 15-600 МПа для производства «сырых» деталей, которые имеют все необходимые геометрические характеристики окончательной конструкции. Однако ни точные окончательные размеры детали, ни ее механические характеристики на данный момент неизвестны. Последующий этап термической обработки или «спекания» завершает эти характеристики.
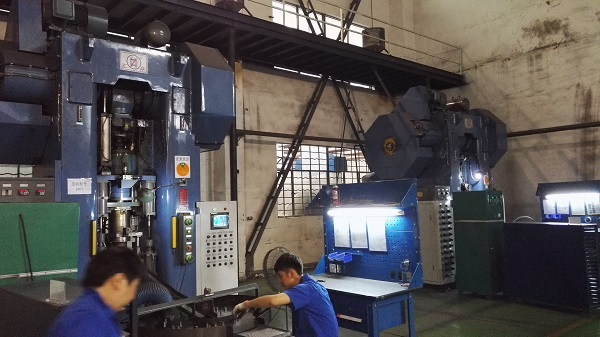
спекание металлов (процесс спекания в порошковой металлургии)
Необработанные детали подаются в печь для спекания до тех пор, пока они не достигнут необходимой конечной прочности, плотности и стабильности размеров. В процессе спекания температура ниже температуры плавления основного порошкового компонента детали нагревается в защищенной среде для молекулярного соединения частиц металлического порошка, составляющих деталь. Увеличиваются размеры и прочность точек контакта между сжатыми частицами, что повышает технические характеристики детали. Чтобы обеспечить конечные параметры компонента, спекание может дать усадку, расширение, улучшить проводимость и/или сделать деталь более прочной в зависимости от конструкции процесса. В печи для спекания компоненты помещаются на непрерывный конвейер и медленно транспортируются по камерам печи для выполнения трех основных задач. Чтобы исключить нежелательные смазки, добавляемые в порошок в процессе уплотнения, детали сначала медленно нагревают. Затем детали поступают в зону высокой температуры печи, где окончательное качество деталей определяется при точно контролируемых температурах в диапазоне от 1450° до 2400°. Тщательно балансируя атмосферу внутри этой печи, добавляются определенные газы, чтобы уменьшить количество существующих оксидов и остановить дополнительное окисление деталей во время этой высокотемпературной фазы. Чтобы завершить детали или подготовить их к каким-либо дополнительным процессам, они наконец проходят через охлаждающую камеру. В зависимости от используемых материалов и размера компонентов весь цикл может занять от 45 минут до 1,5 часов.
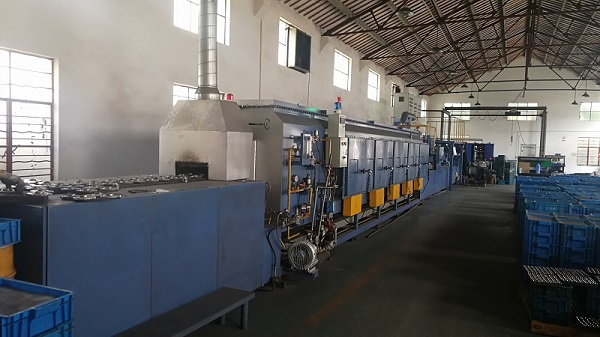
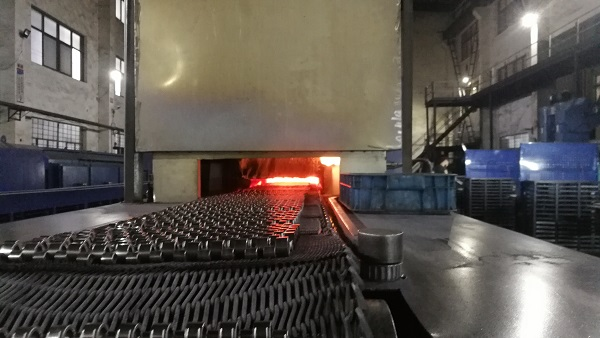
Постобработка
В общем, продукты спекания можно использовать напрямую. Однако для некоторых изделий из спеченного металла, требующих высокой точности, высокой твердости и износостойкости, требуется обработка после спекания. Последующая обработка включает прецизионное прессование, прокатку, экструзию, закалку, закалку поверхности, погружение в масло и пропитку.
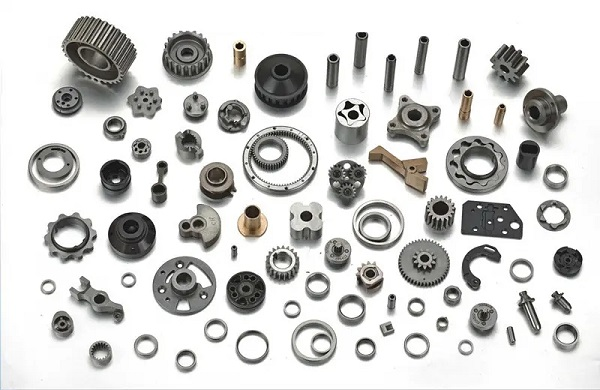
Процесс обработки поверхности порошковой металлургии
Вы можете столкнуться с продуктами порошковой металлургии, шестернями порошковой металлургии, которые легко ржавеют, легко царапаются и т. д., чтобы улучшить износостойкость, стойкость к ржавчине, коррозионную стойкость и усталостную прочность деталей порошковой металлургии. Jiehuang будет выполнять поверхностную обработку деталей порошковой металлургии, чтобы сделать их поверхность более функциональной, а также сделать поверхность более уплотненной. Итак, каковы процессы обработки поверхности порошковой металлургии?
В порошковой металлургии существует пять распространенных процессов обработки поверхности:
1. Покрытие: нанесение слоя других материалов на поверхность обработанных деталей порошковой металлургии без какой-либо химической реакции;
2. Метод механической деформации: поверхность обрабатываемых деталей порошковой металлургии механически деформируется, главным образом, для создания остаточного напряжения сжатия и увеличения поверхностной плотности.
3. Химико-термическая обработка: другие элементы, такие как C и N, диффундируют в поверхность обработанных деталей;
4. Термическая обработка поверхности: фазовый переход происходит за счет циклического изменения температуры, что изменяет микроструктуру поверхности обрабатываемой детали;
5. Химическая обработка поверхности: химическая реакция между поверхностью обрабатываемой детали порошковой металлургии и внешним реагентом;
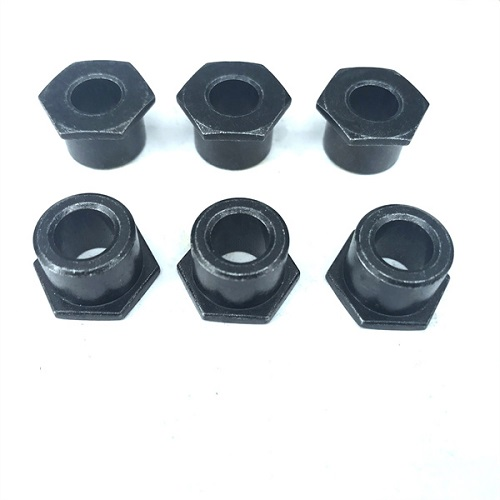
ВЫСОКОКАЧЕСТВЕННЫЕ МЕТАЛЛИЧЕСКИЕ ДЕТАЛИ – НАША СПЕЦИАЛИЗАЦИЯ ДЛЯ ШИРОКИХ ОТРАСЛЕЙ. НАШИ РЕШЕНИЯ ПОДХОДЯТ ДЛЯ ВСЕГО, ВКЛЮЧАЯ ТЯЖЕЛЫЕ ЧАСТИ ПЕРЕДАЧИ ЭНЕРГИИ И ДЕЛИКАТНОЕ МЕДИЦИНСКОЕ ОБОРУДОВАНИЕ.
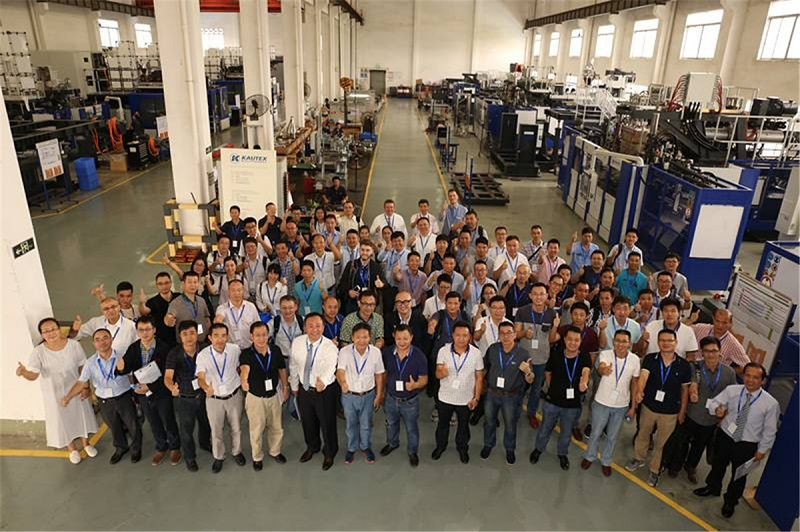