HOW TO DESIGN FOR THE PRODUCTION OF POWDER METAL PARTS
Dear friend, you can use these powder metal design hints to help you create a component that makes the most of powder metallurgy technology. This is not meant to be a comprehensive manual for designing powder metal parts. However, adhering to these guidelines will improve manufacturing efficiency while lowering tooling costs. Contact Jiehuang as powder metallurgy company as soon as possible so that we can help you get the most out of your powder metal components for P/M production. You could also contrast the production of powder metal with other available manufacturing techniques. Utilize our knowledge to meet and surpass your manufacturing objectives. To begin, get in touch with us immediately. Our passion is powder metal design, and we can help!
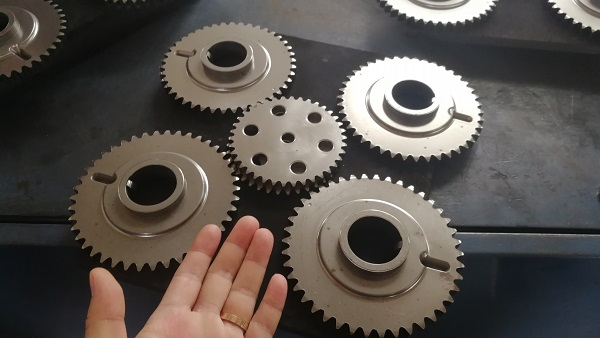
POWDER METAL MATERIALS
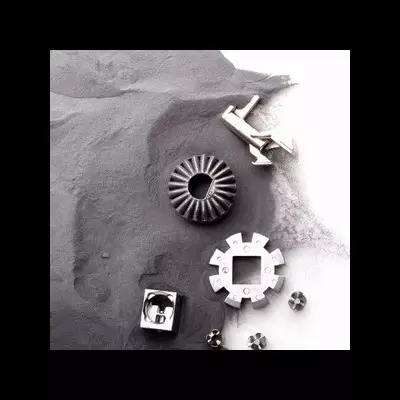
Iron-based powder metallurgy materials
Iron-based powder metallurgy materials are mainly composed of iron elements, and a class of iron and steel materials formed by adding alloying elements such as C, Cu, Ni, Mo, Cr, and Mn. Iron-based products are the most productive type of materials in the powder metallurgy industry.
1. Iron-based powder
The powders used in powder metallurgy iron-based materials and products mainly include pure iron powder, iron-based composite powder, iron-based pre-alloyed powder, etc.
2. PM iron-based products
Conventional pressing/sintering technology can generally produce iron-based products with a density of 6.4~7.2g/cm3, which are used in automobiles, motorcycles, home appliances, electric tools and other industries, with the advantages of shock absorption, noise reduction, light weight and energy saving.
3. Powder injection molding (MIM) iron-based products
Metal powder injection molding (MIM) uses metal powder as raw material to manufacture small metal parts with complex shapes by means of plastic injection molding process. In terms of MIM materials, 70% of the materials currently used are stainless steel and 20% are low-alloy steel materials. MIM technology is widely used in mobile phone, computer and auxiliary equipment industries, such as mobile phone SIM clips, camera rings, etc.
Powder metallurgy cemented carbide
Cemented carbide is a powder metallurgy hard material with transition group refractory metal carbide or carbonitride as the main component. Because of its good strength, hardness and toughness matching, cemented carbide is mainly used as cutting tools, mining tools, wear-resistant parts, top hammers, rolls, etc., and is widely used in steel, automobile, aerospace, CNC machine tools, machinery industry Mould, marine engineering equipment, rail transit equipment, electronic information technology industry, construction machinery and other equipment manufacturing and processing and mining, oil and gas resource extraction, infrastructure construction and other industries.
Powder metallurgy magnetic material
Magnetic materials prepared by powder molding and sintering methods can be divided into two categories: powder metallurgy permanent magnetic materials and soft magnetic materials. Permanent magnet materials mainly include samarium cobalt rare earth permanent magnet materials, neodymium, iron, boron permanent magnet materials, sintered AlNiCo permanent magnet materials, ferrite permanent magnet materials, etc. Powder metallurgy soft magnetic materials mainly include soft ferrite and soft magnetic composite materials.
The advantage of powder metallurgy to prepare magnetic materials is that it can prepare magnetic particles in the size range of single domain, achieve consistent orientation of magnetic powder during the pressing process, and directly produce high magnetic energy product magnets close to the final shape, especially for hard-to-machine hard and brittle magnetic materials. In terms of materials, the advantages of powder metallurgy are more prominent.
Powder metallurgy superalloys
Powder metallurgy superalloys are based on nickel and are added with various alloying elements such as Co, Cr, W, Mo, Al, Ti, Nb, Ta, etc. It has excellent high temperature strength, fatigue resistance and hot corrosion resistance and other comprehensive properties. The alloy is the material of key hot-end components such as aero-engine turbine shafts, turbine disk baffles, and turbine disks. The processing mainly involves powder preparation, thermal consolidation molding, and heat treatment.
Our professional team will advise on materials based on the properties of your powder metal parts.The vast range of raw materials that may be used to satisfy your needs in terms of price, durability, quality control, and specific applications is one of the main benefits of employing powder metal to produce components. Iron, steel, tin, nickel, copper, aluminum, and titanium are among the metals that are frequently used. It is possible to use refractory metals including bronze, brass, stainless steel, and nickel-cobalt alloys, as well as tungsten, molybdenum, and tantalum. The Powder Metal process includes combining various metals to create unique alloys that are tailored to your application's requirements. We can assist you in designing self-lubrication, corrosion resistance, and other qualities as a crucial component of the manufacturing process in addition to strength and hardness qualities. We can press complex structures using these unique mixtures of metal powders at production rates of up to 100 pieces per minute.
Pressing
It is put into a vertical hydraulic or mechanical press where it is deposited in a tool steel or carbide die once the appropriate alloy of powders has been mixed. JIEHUANG can press components with up to four distinct levels of fine detail. Depending on the size and density requirements, this method uses 15-600MPa pressure to produce "green" parts that have all of the required geometric characteristics of the final design. However, neither the part's precise final dimensions nor its mechanical characteristics are present at this time. The subsequent heat treatment, or "sintering," step completes those features.
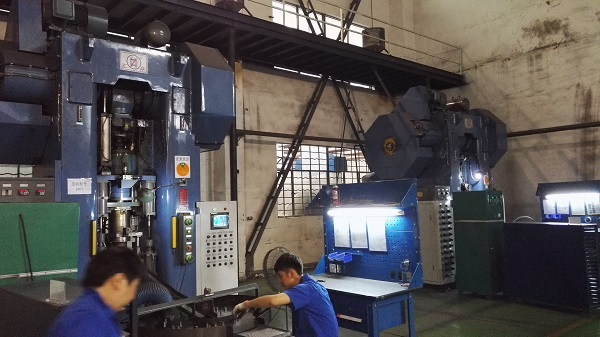
metal sintering (sintering process in powder metallurgy)
The green pieces are fed into a sintering furnace until they reach the necessary final strengths, densities, and dimensional stability. In the process of sintering, temperatures below the melting point of the main powder component of the part are heated in a protected environment to molecularly connect the metal powder particles that make up the part. The size and strength of the contacts points between the compressed particles grow to enhance the component's technical characteristics. In order to meet the final component parameters, sintering might shrink, expand, improve conductivity, and/or make the part tougher depending on the process design. In a sintering furnace, the components are put on a continuous conveyor and slowly transported through the furnace's chambers to accomplish three main tasks. To eliminate undesired lubricants added to the powder during the compaction process, the pieces are first slowly heated. The parts next proceed to the high heat zone of the furnace, where the final qualities of the parts are determined at precisely controlled temperatures ranging from 1450° to 2400°. By carefully balancing the atmosphere inside this furnace chamber, certain gases are added to decrease existing oxides and stop additional oxidation of the parts during this high heat phase. To complete the pieces or get them ready for any additional processes, they finally go through a cooling chamber. Depending on the materials used and the size of the components, the entire cycle may take 45 minutes to 1.5 hours.
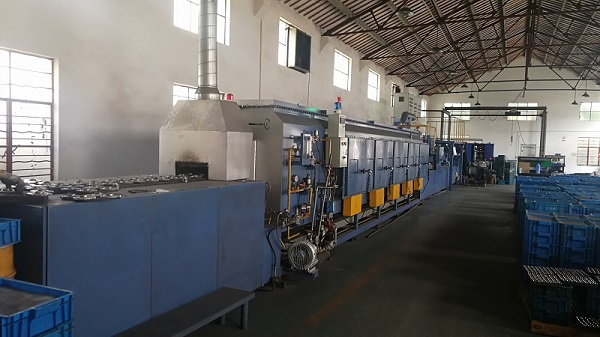
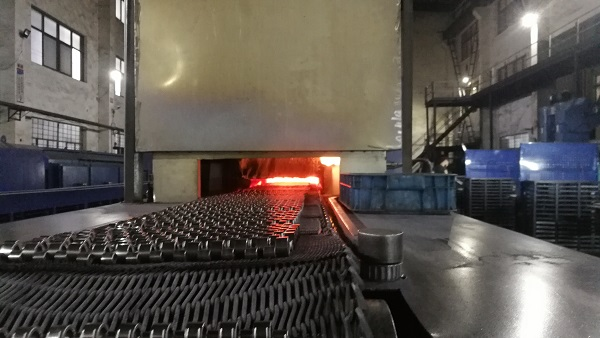
post-processing
In general, the sintering products can be used directly. However, for some sinter metal products that require high precision and high hardness and wear resistance, post-sintering treatment is required. Post-processing includes precision pressing, rolling, extrusion, quenching, surface quenching, oil immersion, and infiltration.
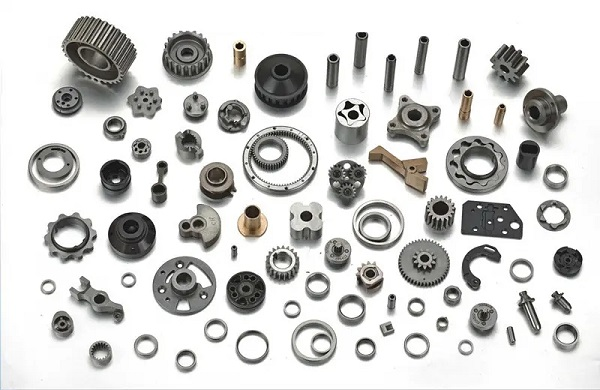
Surface treatment process of powder metallurgy
You may encounter powder metallurgy products, powder metallurgy gears that are easy to rust, easy to scratch, etc., in order to improve the wear resistance, rust resistance, corrosion resistance and fatigue strength of powder metallurgy parts. Jiehuang will carry out surface treatment on powder metallurgy parts, which is to make its surface more functional, and also to make the surface more densified. So what are the powder metallurgy surface treatment processes?
There are five common surface treatment processes in powder metallurgy:
1. Coating: Coating a layer of other materials on the surface of the processed powder metallurgy parts without any chemical reaction;
2. Mechanical deformation method: The surface of the powder metallurgy parts to be processed is mechanically deformed, mainly to generate compressive residual stress and to increase the surface density.
3. Chemical heat treatment: other elements such as C and N diffuse into the surface of the treated parts;
4. Surface heat treatment: the phase change occurs through the cyclic change of temperature, which changes the microstructure of the surface of the treated part;
5. Surface chemical treatment: the chemical reaction between the surface of the powder metallurgy part to be treated and the external reactant;
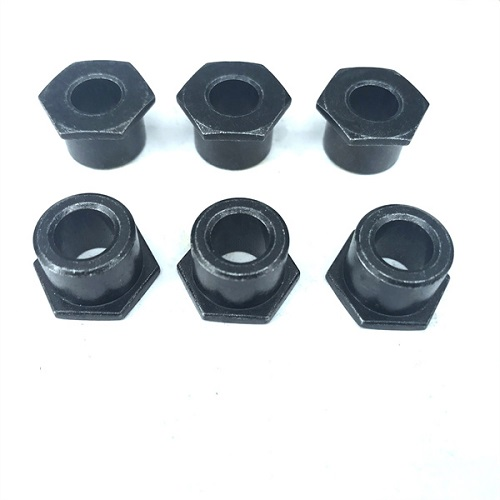
HIGH QUALITY POWDERED METAL PARTS ARE OUR SPECIALTY FOR A WIDE VARIETY OF INDUSTRIES. OUR SOLUTIONS ARE SUITABLE FOR EVERYTHING, INCLUDING HEAVY DUTY POWER TRANSMISSION PARTS AND DELICATE MEDICAL EQUIPMENT.
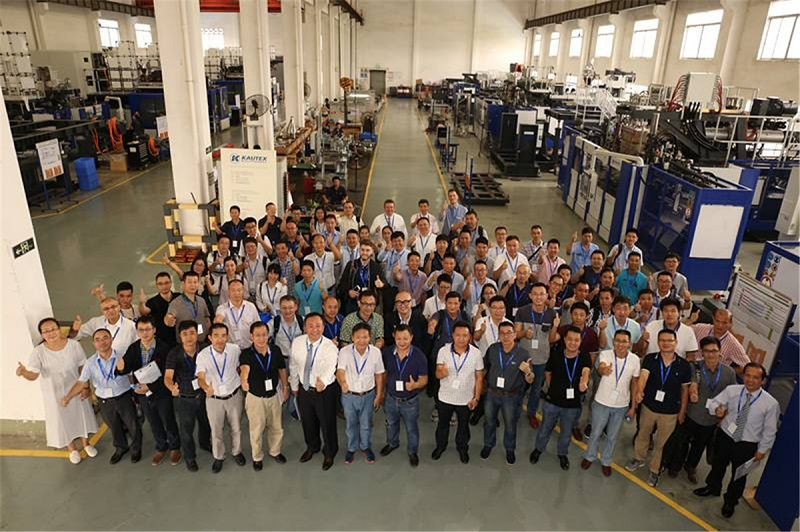